Fronius TransSynergic 7200
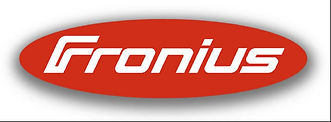
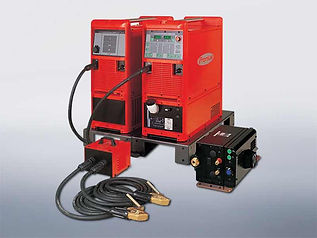
-
Output up to 720 A
-
For automated and robot applications
The powerful power sources are based on a tried and tested solution: two digitally controlled TransSynergic 4000s are connected via a high-speed data interface, achieving a combined output of 720 A.
The parallel-connected Duo is designed for high deposition rates, as required in automated and robotic applications.
3 - 720 A
60 % d.c. at 720 A,100 % d.c. at 640 A
35,2 kg / 77.6 lb
2 x 3 x 400 V
Process
MIG/MAG
Base metals
-
Aluminium
-
CrNi
-
Special metals
-
Steel
Fields of use
-
Automobile and component supply industry
-
Industrial plants, pipeline construction, assembly companies
-
Manufacture of special vehicles and construction machinery
-
Plant, container and machine construction, steel engineering
-
Rail vehicle construction
-
Robotic welding
-
Shipbuilding / offshore
Overview
-
Earth fault monitor
Prevents the welding current from flowing over the earth wire, which would destroy the PE conductor system -
Energy-saving inverter technology
For higher degrees of efficiency, lower weight and smaller dimensions -
Job mode
Once perfected, machine settings can be saved and called up at any time. -
Microprocessor controlled
for easy operation -
Remote control facility
Enables user to intervene in the welding process directly on-site and change parameters -
Synergic operation
For optimum welding parameters. Simply select material and sheet thickness and the stored know-how controls the welding process automatically
Equipment features
General
General
-
"S" mark, CE mark as standard
-
Anti-stick function
-
Automatic burn-back correction
-
Automatic cooling unit shutdown
-
Automatic gas post-flow time (welding current-dependent)
-
Burn-back pulse (perfect wire end, optimum re-ignition)
-
Cellulose-compatible
-
Continuous welding current adjustment using TIG welding torch
-
Digital welding process control
-
Earth fault monitor
-
Energy-saving inverter technology
-
Expansion using modules
-
Feeder inching - no gas or current
-
Gas test function
-
Hot start
-
Job mode
-
Microprocessor controlled
-
Overtemperature protection
-
Remote control facility
-
Synergic operation
-
TIG Comfort stop
-
Temperature-controlled fan
-
Wire feeder creep
-
free parameter selection on the welding torch
Operating modes
-
2-step mode, 4-step mode
-
Spot welding
-
TIG
-
Welding start aluminium (special 4-step mode)
Displays
-
Final (i.e. "end") current
-
Hold function Automatically saves the actual values when welding finishes
-
Intermediate arc
-
Mains voltage monitor
-
Operating mode
-
Overtemperature
-
Service codes
-
Sheet thickness
-
Welding current
-
Welding current (actual value)
-
Welding current (standard value)
-
Welding voltage
-
Welding voltage (actual value)
-
Welding voltage (standard value)
-
Wire feed speed
Settabel Parameters
-
Arc length correction
-
Burn-back time
-
Dynamic
-
Final (i.e. "end") current
-
Gas post-flow time
-
Gas pre-flow time
-
Spot-welding time
Options
Displays
-
"a" dimension
-
Arc length
-
Job number
-
Manual mode
-
Motor current
-
Welding speed
General
-
Current flow signal
-
Flow watchdog for torch cooling
-
Hosepack holder - Human
-
Keylock switch
-
PullMig mode
-
Robot interface, analog
-
Robot interface, digital
-
Spatter-free ignition
-
Touchdown ignition
-
Welding programs from database
Process
Process
-
MIG brazing
-
MIG/MAG Standard
-
MIG/MAG high performance welding
-
TIG DC
Base materials
Recommended ground materials
-
Aluminium
-
CrNi
-
Special metals
-
Steel
Application area/sector
Recommended areas of use
-
Automobile and component supply industry
-
Industrial plants, pipeline construction, assembly companies
-
Manufacture of special vehicles and construction machinery
-
Plant, container and machine construction, steel engineering
-
Rail vehicle construction
-
Robotic welding
-
Shipbuilding / offshore
Technology
· Digital Revolution
To see the benefits of the digital revolution in welding technology, let’s try listening first: to some music. Why? Simple: Not so very long ago, the good old vinyl record was the most important medium. The only problem was that it soon reached its limits in terms of quality. The more frequently it was played, the more the sound quality deteriorated. With digital technology, music remains music no matter how often a song is played. The quality remains the same. The same applies to Fronius digital welding technology: 100 % reproducible welding results. Again and again. As often as you want. The basis for this is the highest possible precision in the welding process. And it’s completely digitally controlled.