Fronius TransSynergic 4000 C MV
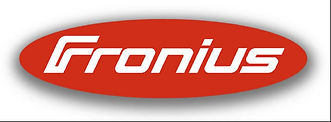

-
Output up to 400 A
-
Multivoltage
-
Microprocessor-controlled synergic operation
-
Multiprocess
The fully digitised and microprocessor-controlled MIG/MAG power source for short circuit arcs and spray arcs enables the best weld properties in every respect, and reproducible results time and time again. With its modular design, the TransSynergic 4000 (400 A) meets the highest demands of the automobile and component supply industry, equipment construction, chemical plant construction, machine and tracked vehicle manufacturing, and in shipyards.
Very easy to operate, thanks to synergic operation: simply select sheet thickness and material at the touch of a button, and the power source then automatically falls back on its embedded expert knowledge to control the entire welding process. The Comfort version supports extra functions such as process selection or saving parameter settings. The Multivoltage version switches between the different mains voltages automatically.
3 - 400 A
50 % d.c. at 400 A,100 % d.c. at 280 - 320 A
35,2 kg / 77.6 lb
3 x 200 - 240 V, 3 x 380 - 460 V
Process
MIG/MAG
Base metals
-
Aluminium
-
CrNi
-
Sondermetalle
-
Stahl
Fields of use
-
Manufacture of special vehicles and construction machinery
-
Metal and gantry construction, fitting shops and forges
-
Plant, container and machine construction, steel engineering
-
Rail vehicle construction
-
Robotic welding
-
Shipbuilding / offshore
Overview
-
Earth fault monitor
Prevents the welding current from flowing over the earth wire, which would destroy the PE conductor system -
Energy-saving inverter technology
For higher degrees of efficiency, lower weight and smaller dimensions -
Job mode
Once perfected, machine settings can be saved and called up at any time. -
Microprocessor controlled
for easy operation -
Multivoltage
guarantees worldwide usability, as it can be switched over to the various mains voltages -
Remote control facility
Enables user to intervene in the welding process directly on-site and change parameters -
Synergic operation
For optimum welding parameters. Simply select material and sheet thickness and the stored know-how controls the welding process automatically
Equipment features
General
General
-
"S" mark, CE mark as standard
-
Anti-stick function
-
Automatic burn-back correction
-
Automatic cooling unit shutdown
-
Automatic gas post-flow time (welding current-dependent)
-
Burn-back pulse (perfect wire end, optimum re-ignition)
-
Carbon gouging
-
Cellulose-compatible
-
Continuous welding current adjustment using TIG welding torch
-
Digital welding process control
-
Earth fault monitor
-
Energy-saving inverter technology
-
Expansion using modules
-
Feeder inching - no gas or current
-
Gas test function
-
Hot start
-
Job mode
-
Microprocessor controlled
-
Multivoltage
-
Overtemperature protection
-
Remote control facility
-
Synergic operation
-
TIG Comfort stop
-
Temperature-controlled fan
-
Wire feeder creep
-
free parameter selection on the welding torch
Operating modes
-
2-step mode, 4-step mode
-
Spot welding
-
TIG
-
Welding start aluminium (special 4-step mode)
Displays
-
Final (i.e. "end") current
-
Hold function Automatically saves the actual values when welding finishes
-
Intermediate arc
-
Mains voltage monitor
-
Operating mode
-
Overtemperature
-
Service codes
-
Sheet thickness
-
Welding current
-
Welding current (actual value)
-
Welding current (standard value)
-
Welding voltage
-
Welding voltage (actual value)
-
Welding voltage (standard value)
-
Wire feed speed
Settabel Parameters
-
Arc length correction
-
Burn-back time
-
Dynamic
-
Final (i.e. "end") current
-
Gas post-flow time
-
Gas pre-flow time
-
Spot-welding time
-
Options
General
-
Current flow signal
-
Flow watchdog for torch cooling
-
Hosepack holder - Human
-
Keylock switch
-
PullMig mode
-
Robot interface, analog
-
Robot interface, digital
-
Spatter-free ignition
-
Touchdown ignition
-
Welding programs from database
-
"a" dimension
-
Arc length
-
Job number
-
Manual mode
-
Motor current
-
Welding speed
-
Process
Process
-
MIG brazing
-
MIG/MAG Standard
-
TIG DC
-
Base materials
Recommended ground materials
-
Aluminium
-
CrNi
-
Sondermetalle
-
Stahl
-
Application area/sector
Recommended areas of use
-
Manufacture of special vehicles and construction machinery
-
Metal and gantry construction, fitting shops and forges
-
Plant, container and machine construction, steel engineering
-
Rail vehicle construction
-
Robotic welding
-
Shipbuilding / offshore
-
Displays