Fronius MagicWave 4000 Job TIG AC/DC
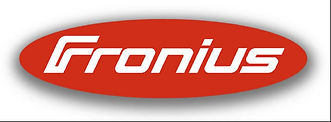

-
400 A output
-
Cold wire control and automated use, robotic welding
-
Welds low-alloy and high-alloy steels, aluminium and non-ferrous metals
The MagicWave 4000 is a fully digitally controlled TIG AC/DC power source with ActiveWave technology, and is characterised by the softest possible yet highly stable arc. It has an output of 400 A, is both light and robust and self-explanatory in operation. The power source can be used in many different fields: chemical, container, machine and plant construction, pipeline construction, automotive and tracked vehicle manufacturing, aerospace industry and shipbuilding, as well as by all types of installation, maintenance and repair companies.
The MagicWave 4000 Job is an extremely powerful and robust welding system. Ideal for use on construction sites, and equally suited to manufacturing. The power source welds aluminium and its alloys, low-alloy and high-alloy steels and non-ferrous metals. The Job version enables cold wire control, as well as automated use and robotic welding.
3 - 400 A
45 % d.c. at 400 A,100 % d.c. at 310 A
58,2 kg / 128.31 lb
3 x 400 V
Process
TIG
Base metals
-
Aluminium
-
CrNi
-
Special metals
-
Steel
Fields of use
-
Aerospace industry
-
Automobile and component supply industry
-
Chemical plant construction
-
Industrial plants, pipeline construction, assembly companies
-
Maintenance and repair
-
Metal and gantry construction, fitting shops and forges
-
Plant, container and machine construction, steel engineering
-
Rail vehicle construction
-
Robotic welding
-
Shipbuilding / offshore
Overview
-
Automatic gas post-flow time (welding current-dependent)
The ideal post-flow time is calculated automatically so that electrode and weld pool do not oxidise -
Automatic tungsten balling
Brings enormous time savings - simply clamp the sharpened electrode, pre-select cap diameter, the arc automatically forms the correct cap size -
Generator-compatible
for mobile use, including construction sites -
Job mode
Once perfected, machine settings can be saved and called up at any time. -
Non-contact ignition (HF)
For perfect arc ignition with high-voltage pulse, even for very long hosepacks -
Reversed polarity ignition
Improves the ignition of the TIG direct current arc -
TIG pulse
For perfect joining of light-gauge sheets during TIG welding -
Touchdown ignition
For ignition with no high-voltage pulses in sensitive applications
Equipment features
General
General
-
"S" mark, CE mark as standard
-
Anti-stick function
-
Automatic cooling unit shutdown
-
Automatic gas post-flow time (welding current-dependent)
-
Automatic tungsten balling
-
Carrying handle
-
Continuous welding current adjustment using TIG welding torch
-
Digital welding process control
-
Earth fault monitor
-
Energy-saving inverter technology
-
Expansion using modules
-
Gas test function
-
Generator-compatible
-
Hosepack holder
-
Hot start
-
Job mode
-
Non-contact ignition (HF)
-
Operating hours counter
-
Overtemperature protection
-
Polarity switching
-
Remote control facility
-
Reversed polarity ignition
-
Soft arc by Active Wave
-
TIG pulse
-
Temperature-controlled fan
-
Touchdown ignition
-
free parameter selection on the welding torch
Operating modes
-
2-step mode, 4-step mode
-
Special 4-step mode
-
Spot welding
Displays
-
Final (i.e. "end") current
-
Hold function Automatically saves the actual values when welding finishes
-
Job number
-
Mains voltage monitor
-
Operating mode
-
Overtemperature
-
Sequence status
-
Service codes
-
Start arc current
-
Welding current (actual value)
-
Welding voltage (actual value)
Settabel Parameters
-
AC balance
-
AC frequency
-
AC waveform
-
Downslope
-
Dynamic
-
Electrode diameter
-
Falling characteristic
-
Final (i.e. "end") current
-
Gas post-flow time
-
Gas pre-flow time
-
Spot-welding time
-
Start arc current
-
Stepless welding power
-
TAC (tacking acc. to program)
-
TIG pulse
-
UpSlope
Options
General
-
Cold wire control
-
Current flow signal
-
Flow watchdog for torch cooling
-
Keylock switch
-
Robot interface, analog
-
Robot interface, digital
Process
Process
-
TIG AC/DC
-
TIG DC
Base materials
Recommended ground materials
-
Aluminium
-
CrNi
-
Special metals
-
Steel
Application area/sector
Recommended areas of use
-
Aerospace industry
-
Automobile and component supply industry
-
Chemical plant construction
-
Industrial plants, pipeline construction, assembly companies
-
Maintenance and repair
-
Metal and gantry construction, fitting shops and forges
-
Plant, container and machine construction, steel engineering
-
Rail vehicle construction
-
Robotic welding
-
Shipbuilding / offshore